Lithium Extraction Methods
Discover the different lithium extraction methods: exploring greener alternatives and the game-changing technology of Lithium Harvest.
Lithium Extraction Methods - From Traditional to Innovative Approaches
Often called the "white gold" of the energy revolution, lithium powers everything from electric vehicles and renewable energy storage to smartphones and laptops. But while demand is soaring, traditional extraction methods - like evaporation ponds and hard rock mining - are under growing scrutiny for their environmental toll.
Just consider this: extracting a single ton of lithium using conventional methods can consume nearly 500,000 gallons of water - enough to supply a family of four for over three years. And hard rock mining? It can take up 115 acres of land per 1,000 metric tons of lithium carbonate - roughly 87 football fields worth of disruption.
With global demand set to skyrocket, the need for sustainable, scalable solutions has never been more urgent.
Fortunately, innovation is catching up. Direct Lithium Extraction (DLE) and other next-generation technologies are reshaping the landscape, offering faster, cleaner, and far more efficient alternatives.
In this article, we’ll explore the different lithium extraction methods, break down their pros and cons, and show how Lithium Harvest’s breakthrough technology is transforming what was once considered waste into one of the most sustainable sources of lithium on Earth.
Table of contents:
- What Is Lithium Extraction?
- Where Is Lithium Extracted?
- Solar Evaporation Brine Extraction - A Water-Intensive Process
- Hard Rock Mining - A High-Impact, Energy-Intensive Process
- Direct Lithium Extraction (DLE) from Brine - A Cleaner, More Efficient Alternative
- Lithium Extraction from Geothermal Brine - A Sustainable Energy-Tied Solution
- Other Emerging Lithium Extraction Methods
- The Future of Lithium Supply - A Multi-Sourced Approach
- Lithium Production Technologies - A Comparison
- A More Efficient & Sustainable Way - Lithium Extraction From Oilfield Wastewater
- Direct Lithium Extraction - But Different
- Leading the Charge in Eco-Friendly Lithium
- Leading Sustainable Solution With a Powerful Business Case
- Which Extraction Method is the Most Sustainable?
- Lithium Harvest's Patented Lithium Extraction Technology
Prefer to Watch Instead?
Watch this short video from CERAWeek 2025, where our CEO, Sune Mathiesen, breaks down the primary lithium extraction methods - from hard rock mining and solar evaporation to advanced Direct Lithium Extraction - and explains how Lithium Harvest is redefining the future with our revolutionary solution.
What Is Lithium Extraction?
Lithium extraction is the process of obtaining lithium, a highly sought-after alkali metal used in electric vehicles, renewable energy storage, and consumer electronics. Unlike other metals, lithium doesn’t occur in its pure form in nature. Instead, it exists as salts or compounds in underground deposits, brine, mineral ores, clay, seawater, and geothermal fluids.
With global demand for lithium soaring, a sustainable and scalable supply has become a top priority. Historically, two primary methods have dominated the industry:
- Solar Evaporation from Brine: Lithium-rich brine is pumped into vast evaporation ponds, where the sun concentrates lithium over 12–36 months. This method is standard in South America’s “Lithium Triangle,” but it is both land- and water-intensive, with low recovery rates.
- Hard Rock Mining: Lithium-bearing minerals like spodumene are extracted, crushed, and chemically processed. This approach is energy-intensive, environmentally disruptive, and generates significant chemical waste.
In recent years, a new alternative has emerged: Direct Lithium Extraction (DLE). DLE enables lithium to be extracted directly from brine and other lithium-rich sources with greater efficiency and a much smaller environmental footprint.
As EV adoption and energy storage accelerate, DLE technologies are critical to building a reliable and sustainable lithium supply. While legacy players dominate the current market, these innovations are opening new opportunities for cleaner, more efficient extraction, helping to reshape the industry and power the transition to a low-carbon future.
Where Is Lithium Extracted?
Lithium, often called “white gold,” is primarily sourced from two major deposits: mineral-rich hard rock ores and lithium-rich brine reservoirs. Today, global production is heavily concentrated in just a few regions, raising growing concerns about supply chain security.
Global Lithium Production: A Geographically Concentrated Market
- Australia leads global production, contributing 41.3% of global supply in 2023, primarily through hard rock mining.
- Chile, China, and Argentina collectively account for nearly 90% of the world’s lithium, mostly from continental brines.
- The United States, once a dominant player supplying 27% of global lithium in 1996, now produces less than 1%. Recognizing lithium’s strategic importance, the U.S. is now taking decisive steps to rebuild its domestic supply chain.
While Australia excels in hard rock mining, Chile and Argentina tap into vast continental brines. But this heavy reliance on a few regions for such a critical resource presents serious risks, making the need for diversification and sustainable production more urgent than ever.
Why Does This Matter?
A geographically concentrated supply chain poses both economic and geopolitical vulnerabilities, which is why governments and industries around the world are accelerating policy-backed efforts to boost domestic production and secure long-term offtake agreements.
With global lithium demand skyrocketing, the race is on to develop new, sustainable sources - including unconventional deposits like geothermal and oilfield brines. These emerging technologies offer reduced environmental impact and help build a resilient, secure, and diversified lithium future.
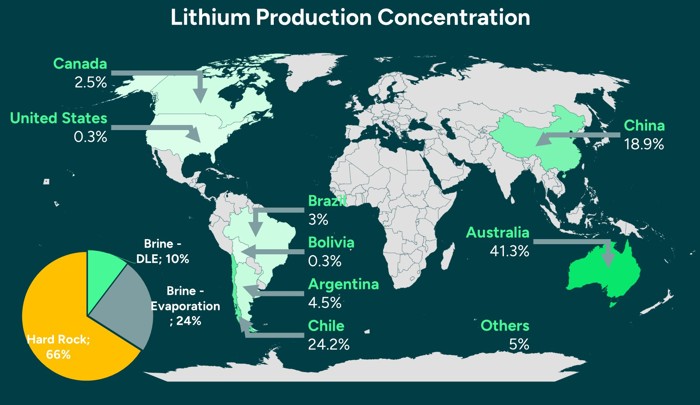
Solar Evaporation Brine Extraction - A Water-Intensive Process
Solar evaporation is one of the most widely used methods for lithium extraction, particularly in South America's lithium-rich salars (salt flats). This process involves pumping lithium-rich brine into massive evaporation ponds, where sunlight gradually evaporates the water over one to two years, leaving behind concentrated lithium salts.
While this method has served as the industry standard for decades, it brings with it significant environmental and efficiency challenges:
- Established process – Commonly used in Chile, Argentina, and Bolivia, where high solar exposure makes the method viable.
- High water consumption – Over 500,000 gallons of water are lost per ton of lithium carbonate equivalent (LCE), worsening water scarcity in already arid regions.
- Large land footprint – Requires up to 65 acres per operation – about 263,000 square meters, equivalent to 210 Olympic-sized swimming pools.
- Slow and inefficient – The process takes two to three years and only recovers 20–40% of the lithium in the brine.
- Chemical waste – Leaves behind large volumes of salt deposits and chemical residues that can contaminate soil and groundwater.
As global lithium demand accelerates, the drawbacks of solar evaporation become increasingly clear. The shift toward faster, cleaner, and more efficient extraction methods is not just desirable - it's essential for a sustainable future.
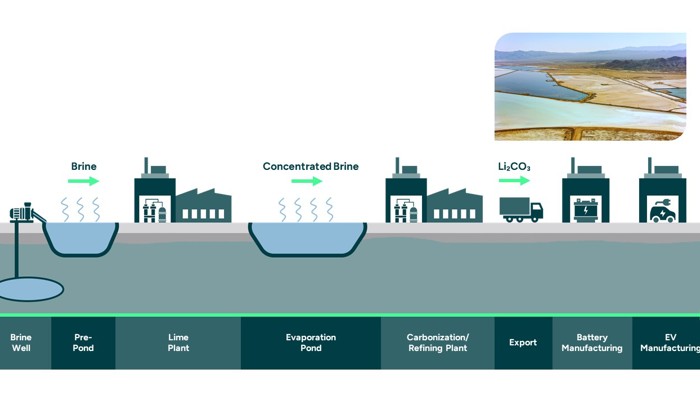
Hard Rock Mining - A High-Impact, Energy-Intensive Process
Hard rock mining is the most common and oldest method of lithium extraction, primarily used in Australia, China, and Canada. This process involves mining lithium-rich spodumene ore from pegmatite deposits, which are clusters of rocks and crystals. The ore undergoes a complex, energy-intensive, and chemically intensive treatment process before the lithium can be used. After mining, the ore is crushed, concentrated, roasted, and leached to obtain lithium concentrate. Much of this concentrate is then shipped to China for final processing, which significantly adds to the carbon footprint and raises questions about waste handling practices.
While hard rock mining ensures a steady lithium supply, it comes with serious environmental and logistical challenges:
- Low lithium yield - Spodumene ore contains only 6–7% lithium, requiring large-scale mining operations to extract a small amount of usable lithium.
- Energy-intensive processing - The roasting and leaching steps demand vast amounts of fuel and electricity.
- High CO₂ emissions - Each ton of lithium extracted emits up to 15 tons (15,000 kg) of CO₂, equivalent to burning 6,522 liters (1,723 gallons) of gasoline, enough to fuel an average car for more than 3.5 years.
- Land disruption - Mining creates large open pits, destroys habitats, and pollutes soil and water sources.
- A complex global supply chain - Reliance on China for final processing increases costs, emissions, and concerns about waste transparency.
The Downside of Hard Rock Lithium Mining
Extracting lithium from hard rock is a high-cost, high-impact process that requires more energy than most alternatives. With growing concerns about carbon emissions, land degradation, and sustainability, the industry is shifting toward cleaner, faster, and more environmentally responsible solutions.
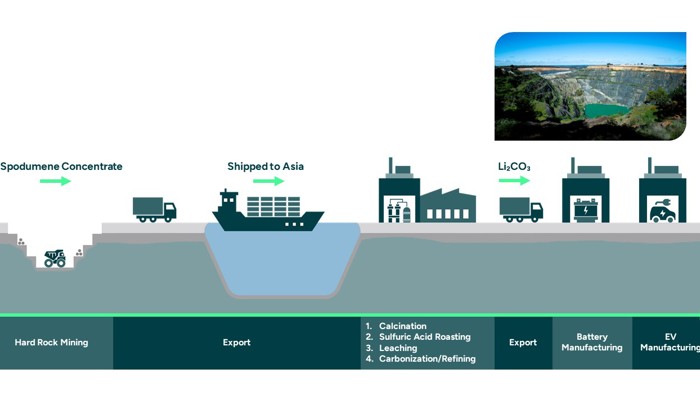
Direct Lithium Extraction (DLE) from Brine - A Cleaner, More Efficient Alternative
Traditional Direct Lithium Extraction (DLE) represents a transformative shift in lithium production, offering a faster, more sustainable alternative to solar evaporation and hard rock mining. Unlike traditional methods, DLE extracts lithium directly from brine sources or evaporation ponds. DLE technologies can be classified into adsorption, ion exchange, and solvent extraction processes. These innovative techniques enable the direct extraction of lithium from complex brines with high concentrations of various ions.
- Higher efficiency – Extracts more lithium with less waste, improving resource utilization.
- Faster production – Cuts lithium extraction time from years to hours, enabling quicker scaling.
- Lower carbon footprint – Uses less energy and eliminates the need for large open-pit mines.
With the growing need for responsible lithium sourcing, DLE is positioning itself as the future of sustainable lithium production.
Learn how Direct Lithium Extraction is revolutionizing sustainable lithium recovery.
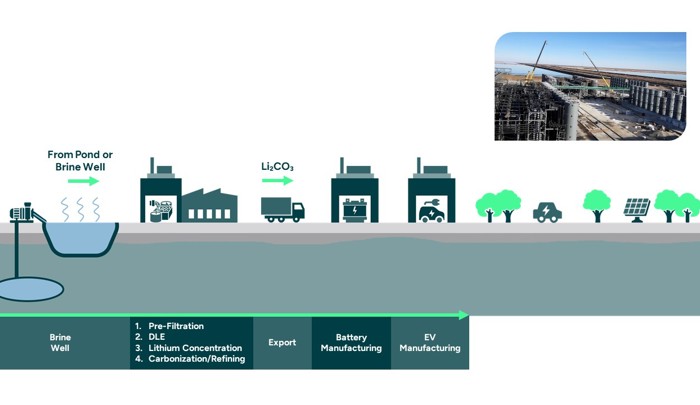
Lithium Extraction from Geothermal Brine - A Sustainable Energy-Tied Solution
Geothermal brine presents a unique, sustainable opportunity for lithium extraction. Unlike conventional methods, geothermal power plants already pump hot, mineral-rich brine from underground reservoirs to generate renewable energy. With efficient lithium extraction, this same brine can be used to extract lithium, without additional environmental disruption.
How It Works
- Brine circulation – Geothermal plants pump hot brine to the surface to produce electricity.
- Lithium separation – Before reinjecting the brine underground, lithium extraction technology selectively extracts lithium or other critical minerals, leaving other minerals and water intact.
- Energy synergy – The process uses renewable geothermal energy, reducing carbon emissions.
Why Geothermal Lithium Extraction Stands Out
- Minimal environmental impact – No open-pit mining, no evaporation ponds, and no groundwater depletion.
- Carbon-neutral lithium – Uses existing geothermal infrastructure, eliminating additional emissions.
- Win-win solution – Geothermal operators generate electricity and/or heat and extract lithium from the same brine source, increasing profitability and sustainability.
Geothermal lithium extraction is already gaining momentum. As the demand for low-carbon lithium grows, this method could become a key solution for securing a domestic, environmentally responsible lithium supply.
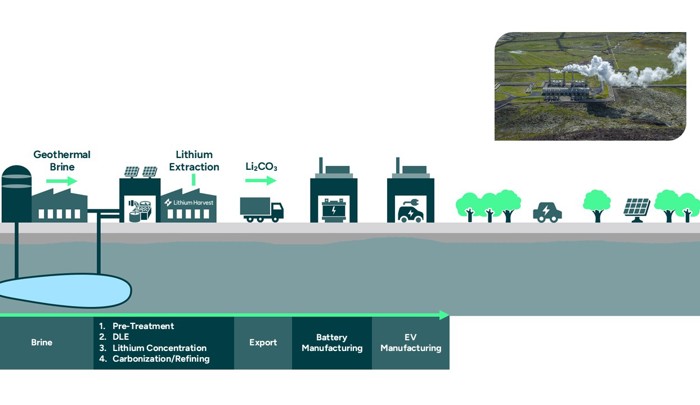
Other Emerging Lithium Extraction Methods
As demand for lithium continues to soar, researchers and companies are exploring new, unconventional sources beyond traditional hard rock mining and brine evaporation. These alternative methods could diversify the lithium supply and reduce environmental impact.
-
Lithium Extraction from Hectorite Clay
Extensive research has been conducted in developing clay processing techniques for lithium extraction, including leaching with acid, alkaline, chloride, and sulfate solutions, water disaggregation, and hydrothermal treatment. However, none of these methods have proven economically viable for extracting lithium from clay on a large scale.
Key challenge: So far, no method has been commercially viable for large-scale lithium production from clay.
-
Lithium from Unconventional Ores (e.g., Lepidolite & Petalite)
Besides spodumene, other lithium-bearing minerals like lepidolite (a lithium-rich mica) and petalite are being exploited, particularly in China and Europe.
- These minerals often require intensive processing, such as acid roasting, similar to clay-based lithium extraction.
- While lower in lithium content, they provide an alternative source that expands supply options.
Key Challenge: Mining and processing low-grade lithium ores is costly, making their commercial viability dependent on lithium prices and process efficiency.
-
Lithium Extraction from Mine Waste and Tailings
Another emerging approach is recovering lithium from waste materials that were previously discarded.
- Tailings from old mining operations, initially processed for borax or other minerals, often contain lithium-rich clays that weren’t extracted before.
- Recovering lithium from waste can reduce environmental impact and extend resource lifespans.
Key Challenge: Lithium concentrations in mine waste are often low, meaning cost-effective and selective extraction methods are required to make this viable.
-
Lithium Extraction from Seawater
The world's oceans contain trillions of tons of lithium, but at very low concentrations (~0.2 mg/l). Existing processes like coprecipitation extraction and hybrid IX-sorption have successfully extracted lithium from seawater, but newer membrane technologies show promise in reducing extraction costs.
Key Challenge: Current technologies remain too expensive and inefficient for commercial-scale production.
-
Lithium Extraction from Oilfield Brines
Produced water from oil and gas operations contains dissolved lithium, presenting a waste-to-resource opportunity:
Key Opportunity: This method leverages existing infrastructure, turning industrial waste into a high-value resource. Learn more about lithium extraction from oilfield brines.
-
Lithium Recycling from Batteries
With the rise in EVs and energy storage systems, recycling end-of-life lithium-ion batteries is a key strategy for sustainability.
- Reduces demand for virgin lithium mining.
- Cuts environmental impact and secures a circular economy.
Key Challenge: Current recycling processes involve high-temperature smelting or chemical leaching, both of which need further efficiency improvements. However, many innovative companies are gaining traction in battery recycling.
The Future of Lithium Supply - A Multi-Source Approach
No single extraction method will solve the lithium supply challenge alone. The future lies in a diversified approach that includes:
- Sustainable brine recovery from geothermal and oilfield sources
- Advanced extraction technologies to boost efficiency, reduce environmental impact, and accelerate production
- Exploration of unconventional lithium extraction methods
- Recycling lithium to support a circular supply chain and meet growing demand
As the industry moves toward cleaner and more efficient lithium production, these emerging methods will play a crucial role in securing a sustainable and responsible lithium supply for the global battery market.
Lithium Production Technologies
Comparison of conventional lithium extraction technologies.
![]() DLE from Brine |
![]() Solar Evaporation Brine Extraction |
![]() Hard Rock Mining |
|
---|---|---|---|
Feedstock | Continental brine | Continental brine | Rock / spodumene |
Project implementation time | 5-7 years | 13-15 years | 8-10 years |
Lithium carbonate production time | 2 hours | 2-3 years | 3-6 months |
Lithium yield | 80-95% | 20-40% | 6-7% |
Average footprint per 1,000 mt LCE | 1.4 acres | 65 acres | 115 acres |
System design | Mobile / stationary | Stationary | Stationary |
Environmental impact | Minimal | Soil- and water contamination | Soil- and water contamination |
Water consumption per 1,000 mt LCE | 80 million gallons | 550 million gallons | 250 million gallons |
CO₂ footprint per 1,000 mt LCE | 1.5 million kg | 5 million kg | 15 million kg |
Average invested capital per 1,000 mt LCE | $45 million | $50 million | $60 million |
Average cost per metric ton | $5,700 | $5,800 | $6,900 |
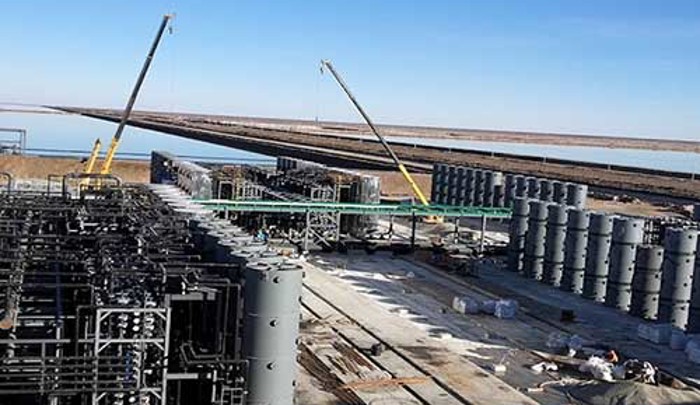
DLE from Brine
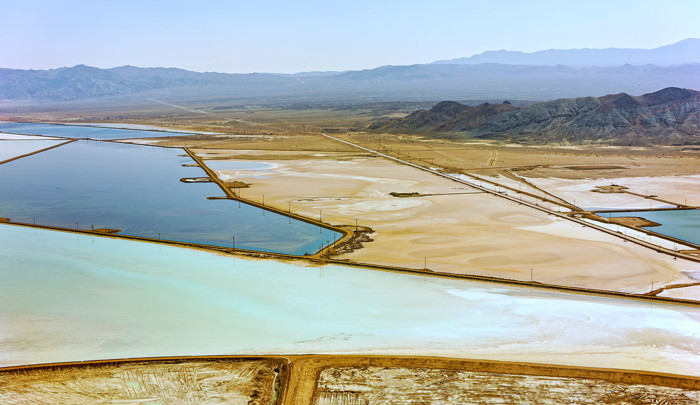
Solar Evaporation Brine Extraction
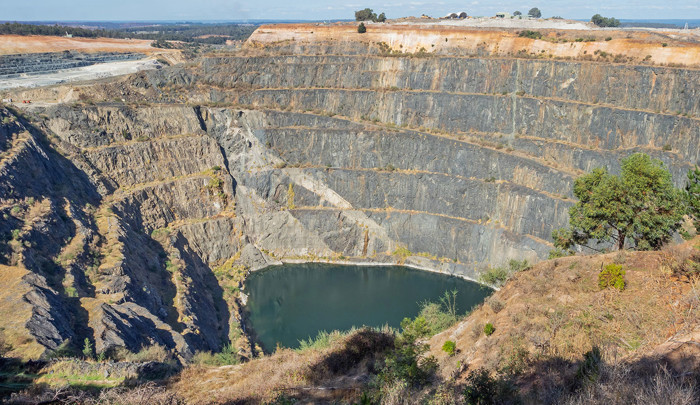
Hard Rock Mining
A More Efficient & Sustainable Solution - Lithium Extraction from Oilfield Wastewater
At Lithium Harvest, we're pioneering a breakthrough lithium extraction solution that transforms oilfield wastewater and geothermal brine into high-quality lithium compounds. Our technology offers a cost-effective, scalable, and environmentally responsible alternative to traditional lithium mining.
Turning Waste into a High-Value Resource
Every year, the oil and gas industry generates millions of barrels of produced water, a costly byproduct that must be managed. Instead of disposing of this water, Lithium Harvest extracts lithium directly from it, creating a new revenue stream for energy companies while reducing environmental impact.
- Uses existing infrastructure - No need for new mines, massive evaporation ponds, or destructive drilling. Our process integrates seamlessly into existing oil and gas operations, turning a waste stream into a valuable resource without expanding the environmental footprint.
- Minimizes land and water use - Hard rock mining requires up to 115 acres per 1,000 metric tons of lithium. In contrast, our compact, modular solution needs only 1.4 acres per ton – about the size of a soccer field.
- Carbon-neutral lithium extraction - While hard rock mining emits 15 tons of CO₂ per ton of lithium carbonate equivalent (LCE), our process is carbon neutral. For context, that's equivalent to 15 one-way economy-class flights from London to New York.
- Reduces operational costs - Oil and gas companies can monetize produced water instead of paying to dispose of it, turning a liability into a revenue stream.
- High lithium recovery rates - Our technology achieves over 95% lithium recovery, significantly outperforming the 20–40% rates typical of solar evaporation.
Unlike traditional methods, which scar landscapes, consume excessive energy, and deplete water resources, our solution is faster, cleaner, and far more efficient. It extracts lithium in hours, not years.
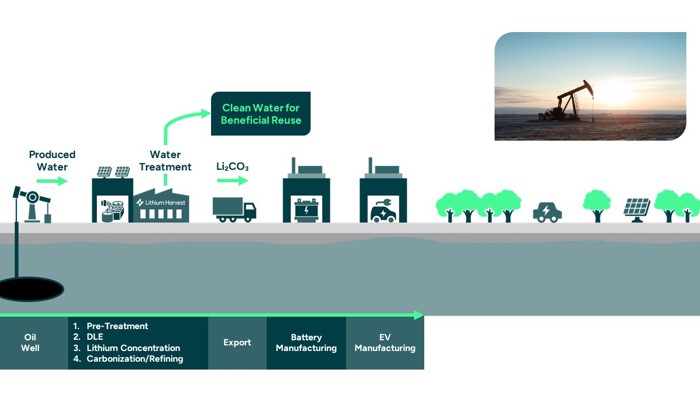
Insights from CERAWeek 2025
Faster. Cleaner. Smarter. Lithium extraction at the source.
In this short video from CERAWeek 2025, CEO Sune Mathiesen introduces Lithium Harvest’s breakthrough lithium extraction technology, which directly extracts lithium from oilfield wastewater. Learn how our scalable, modular solution outperforms traditional mining in cost, recovery rate, and environmental footprint.
Direct Lithium Extraction - But Different
At Lithium Harvest, we've taken Direct Lithium Extraction (DLE) to the next level. While conventional DLE improves efficiency over traditional mining and evaporation, our patented solution, combined with adsorption technology and advanced water treatment, is faster, cleaner, and more scalable than any other lithium extraction method.
The world's demand for sustainable, locally sourced lithium is accelerating, and Lithium Harvest is leading the charge. We're delivering a low-cost, high-yield, and environmentally responsible solution that's poised to transform the lithium supply chain.
![]() Lithium Harvest Solution |
![]() DLE from Brine |
![]() Lithium Harvest Advantage |
|
---|---|---|---|
Feedstock | Produced water / geothermal brine | Continental brine | No drilling permits needed |
Project implementation time | 12-15 months | 5-7 years | No asset acquisition |
System design | Modular and mobile | Mobile / stationary | Unique modular design |
Water consumption | 20 million gallons | 80 million gallons | Water recycled for secondary reuse |
CO₂ footprint | Neutral | 1.5 million kg | Offsets CO₂ footprint from wastewater |
Average invested capital per 1,000 mt LCE | $18 million | $45 million | No land acquisition |
Average cost per metric ton | $4,550 | $5,700 | Low energy technology |
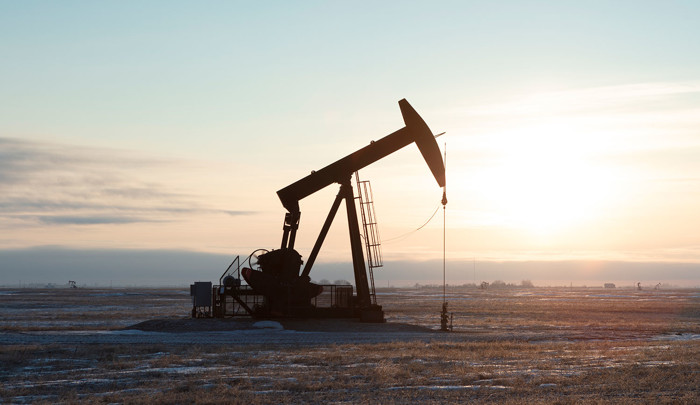
Lithium Harvest Solution
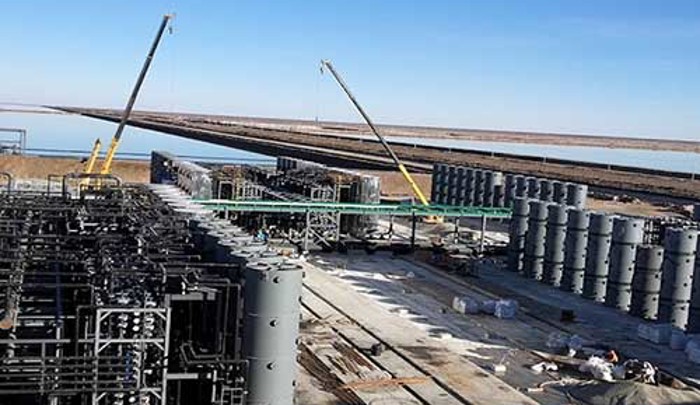
DLE from Brine
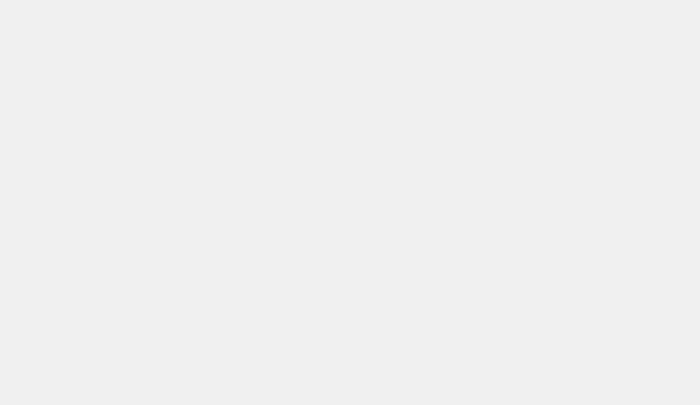
Lithium Harvest Advantage
Leading the Charge in Eco-Friendly Lithium
A New Era of Environmental Responsibility
At Lithium Harvest, we're revolutionizing the lithium industry by combining cutting-edge technology with a deep commitment to sustainability. Unlike traditional lithium extraction methods that drain water resources, destroy landscapes, and emit massive amounts of CO₂, our innovative process is designed to deliver high-purity lithium with minimal environmental impact.
Zero-Carbon, High-Efficiency Lithium
- No CO₂ emissions – While hard rock mining emits 15 tons of CO₂ per ton of lithium, our process is carbon neutral.
- Powered by renewable energy – Our facilities rely on solar energy as the primary power source, significantly reducing the carbon footprint of lithium production.
- Minimal water use – Over 90% of water is recycled, eliminating the need for freshwater extraction and safeguarding local water supplies.
Compact Facility Design: A Smarter Approach to Lithium Extraction
Unlike large-scale mining operations that require open pits, evaporation ponds, and sprawling infrastructure, our modular and compact facilities are designed for:
- Easy integration into existing oilfield and water treatment sites - no need for new land development.
- Rapid deployment - scalable and adaptable to different brine sources.
- Minimal environmental disruption - no excessive pipelines, no waste ponds, and no impact on local wildlife.
Sustainability in Action: Transforming Waste into a Resource
Our process takes produced water from oil and gas operations - a by-product once considered waste - and turns it into a valuable source of lithium. This prevents unnecessary disposal and creates a sustainable lithium supply without additional environmental degradation.
- Separate refining locations are unnecessary. Our extraction and refining operations are strategically located alongside produced water treatment centers, eliminating the energy-intensive transportation of raw materials.
- No waste by-products - our extraction process does not generate any waste by-products, reflecting our commitment to protecting the Earth's vital water resources.
- Offset carbon savings - our low-pressure, energy-efficient process also contributes to offsetting carbon savings through effective water management, making a significant and positive environmental difference.
Advancing Water Conservation: A New Standard for Lithium Production
Water scarcity is a significant concern in lithium extraction, as conventional methods consume vast amounts of freshwater. At Lithium Harvest, our process:
- Uses no freshwater sources, protecting local water supplies.
- Recycles over 90% of process water, reducing waste and ensuring responsible water management.
- Prevents contamination – Unlike hard rock mining and evaporation, which can pollute rivers and groundwater, our method ensures zero water pollution.
A More Responsible Lithium Supply Chain
Sustainable sourcing is no longer optional for EV manufacturers, battery producers, and investors - it's a necessity. By choosing Lithium Harvest's low-carbon, high-efficiency lithium, companies can:
- Reduce battery supply chain emissions by up to 47%.
- Achieve ESG and sustainability goals with a verified, green lithium source.
- Strengthen onsite domestic lithium production.
Lithium is essential for the world's transition to electric vehicles and renewable energy, but not all lithium is created equal. Lithium Harvest is redefining what it means to produce lithium responsibly.
With a zero-carbon footprint, unparalleled efficiency, and a fully circular approach to resource management, we prove that innovation, sustainability, and profitability can go hand in hand.
A Sustainable Lithium Solution with a Powerful Business Case
At Lithium Harvest, sustainability is about more than reducing environmental impact - it's about delivering a commercially viable, scalable, and high-yield lithium extraction solution.
By leveraging produced water from oil and gas operations or geothermal brine, we offer a low-cost, high-efficiency alternative that outperforms traditional lithium extraction methods both financially and operationally.
Lower Capital Costs, Higher Returns
- No need for costly land acquisition –our modular plants integrate directly into existing oil and gas infrastructure.
- No drilling permits are required – unlike traditional lithium projects that require extensive permitting, our solution bypasses new drilling.
- Minimal upfront investment – our streamlined approach reduces CapEx by up to 70%, allowing for faster and more cost-effective project deployment.
Unmatched Operational Efficiency
- >95% lithium recovery rate – far surpassing solar evaporation's 20-40% efficiency.
- Fastest lithium extraction process – converts produced water into battery-grade lithium in hours, not years.
- Low energy consumption – our low-pressure, fully automated, energy-efficient system keeps operational costs low while maximizing output.
- Cost-effective operation - our on-site production and refining process, coupled with fixed-price feedstock, ensures the cost-effective production of lithium compounds.
A Scalable, Fast-to-Market Solution
Unlike conventional lithium projects that take years to develop, Lithium Harvest's modular plants are:
- Rapidly deployable – designed for fast implementation and quick scalability
- Adaptable to different brine sources – our technology is compatible with oilfield, geothermal, and other lithium-rich brines.
- Flexible production – our facilities can be scaled up or down based on market demand.
Monetizing a Wasted Resource
Produced water has long been a costly liability for oil and gas companies. Lithium Harvest turns this waste stream into a high-value lithium source, offering a win-win opportunity for the energy industry.
- New revenue streams – instead of paying for wastewater disposal, companies can profit from lithium extraction.
- Strengthened ESG positioning – demonstrates commitment to sustainability and responsible resource management.
- No disruption to core business – our solution operates alongside existing oilfield operations, requiring minimal modifications.
Which Lithium Extraction Method is the Most Sustainable?
As demand for lithium skyrockets, choosing the right extraction method is critical for environmental sustainability. Traditional methods, such as hard rock mining and solar evaporation, come with significant environmental drawbacks, while newer technologies like Direct Lithium Extraction (DLE) pave the way for a cleaner and more efficient future.
The Environmental Cost of Traditional Lithium Extraction
Hard Rock Mining - Extremely energy-intensive, requiring high-temperature processing and consuming vast amounts of fuel and electricity. This results in:
- High CO₂ emissions - 15 tons of CO₂ per ton of lithium - lead to a greater carbon intensity per unit of lithium extracted.
- Significant land degradation - open-pit mining destroys ecosystems, increases erosion, and leaves behind barren landscapes.
- Severe water pollution - toxic chemical waste from refining processes can contaminate rivers, groundwater, and soil.
Solar Evaporation - While leveraging solar energy, this method still presents critical environmental challenges:
- Requires massive land areas - over 65 acres per ton of lithium, making it highly disruptive to local ecosystems.
- Consumes extreme amounts of water - a significant concern in drought-prone areas, where millions of gallons of water are lost to evaporation.
- Produces harmful waste salts - disposing of these residual minerals can lead to long-term soil and water contamination.
Standard DLE methods, while more efficient and less water-intensive than the above, can still be improved. Lithium Harvest's advanced DLE technology revolutionizes this space by integrating superior water treatment processes, turning a waste product - oil & gas wastewater - into a valuable lithium feedstock.
Our advanced DLE solution focuses on maximizing lithium recovery while minimizing environmental disturbance. It supports a circular economy by repurposing industrial by-products and integrates with existing infrastructure, such as geothermal and oilfield operations, to further reduce environmental impact. This approach yields a higher concentration of lithium, more efficiently and more sustainably.
The world's transition to renewable energy and electric vehicles requires a truly sustainable lithium supply chain. Lithium Harvest is leading this transformation by delivering a solution that is not only environmentally responsible but also economically viable.
Why settle for outdated methods when a cleaner, faster, and more sustainable alternative already exists?
Check out the comparison table below to see the differences and form your own opinion.
![]() Lithium Harvest Solution |
![]() DLE from Brine |
![]() Solar Evaporation Brine Extraction |
![]() Hard Rock Mining |
|
---|---|---|---|---|
Feedstock | Produced water / geothermal brine | Continental brine | Continental brine | Rock / spodumene |
Project implementation time | 12-15 months | 5-7 years | 13-15 years | 8-10 years |
Lithium carbonate production time | 2 hours | 2 hours | 2-3 years | 3-6 months |
Lithium yield | >95% | 80-95% | 20-40% | 6-7% |
Average footprint per 1,000 mt LCE | 1.4 acres | 1.4 acres | 65 acres | 115 acres |
System design | Modular and mobile | Mobile / stationary | Stationary | Stationary |
Environmental impact | Minimal | Minimal | Soil- and water contamination | Soil- and water contamination |
Water consumption per 1,000 mt LCE | 20 million gallons | 80 million gallons | 550 million gallons | 250 million gallons |
CO₂ footprint per 1,000 mt LCE | Neutral | 1.5 million kg | 5 million kg | 15 million kg |
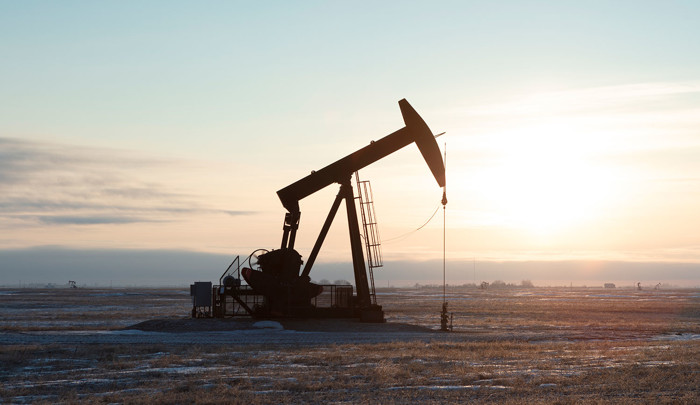
Lithium Harvest Solution
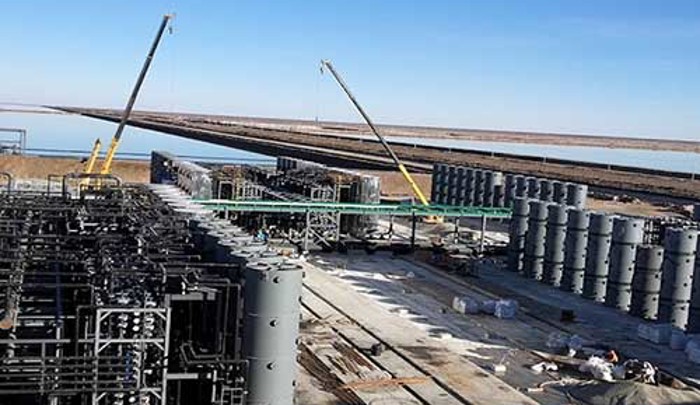
DLE from Brine
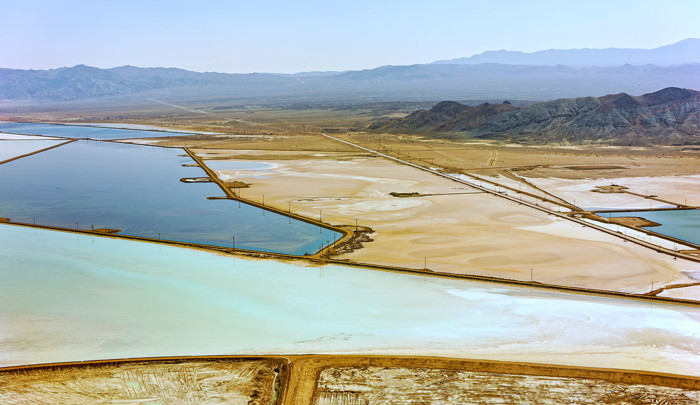
Solar Evaporation Brine Extraction
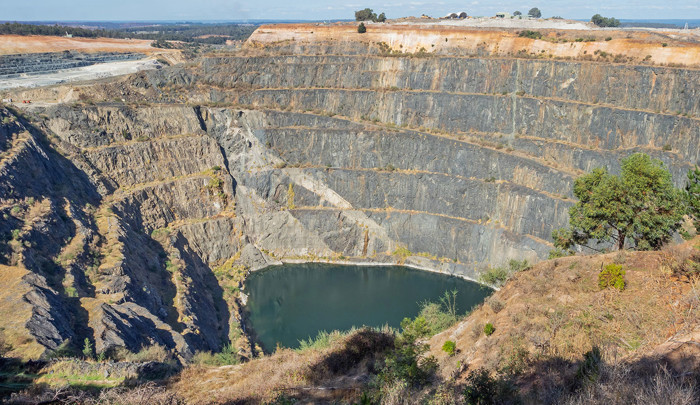
Hard Rock Mining
Lithium Harvest's Patented Lithium Extraction Technology
In conclusion, the sustainability of lithium extraction methods is a critical consideration in pursuing a cleaner and greener future. While traditional methods like hard rock mining and solar evaporation have significant environmental drawbacks, Direct Lithium Extraction (DLE) offers a promising solution.
At Lithium Harvest, we’re at the forefront of this innovative approach. Our patented solution, using our extraction and treatment expertise, allows us to recover lithium and other critical minerals from produced water and other brine sources. By transforming wastewater and byproducts into valuable resources, we’re addressing the environmental challenges of lithium extraction while conserving freshwater supplies.
With our sustainable extraction process, we significantly reduce water consumption, carbon emissions, and ecological impact. By maximizing resource efficiency and minimizing waste, our technology aligns with the principles of a circular economy, helping to create a more sustainable lithium supply chain.
As we continue to advance our proprietary DLE and water treatment solutions, we’re committed to driving the green energy transition and building a better future. By extracting lithium and other critical minerals from produced water, we meet global demand without repeating the mistakes of traditional mining.
A More Sustainable Future Starts Now
Lithium is essential for the global energy transition, but extracting it should not harm our planet.
Not all lithium is created equal - and neither are extraction methods. At Lithium Harvest, we’ve developed a patented Direct Lithium Extraction (DLE) process that’s faster, cleaner, and more efficient than any traditional method.
Our next-generation lithium extraction solution transforms oilfield wastewater and geothermal brine into high-purity lithium - efficiently, sustainably, and at scale. By leveraging existing infrastructure, we eliminate the need for new mines, evaporation ponds, or extensive land use, offering a cost-effective and ESG-friendly solution for energy producers and battery manufacturers.
Why settle for outdated, destructive methods when a better alternative exists? Ready to rethink lithium extraction?
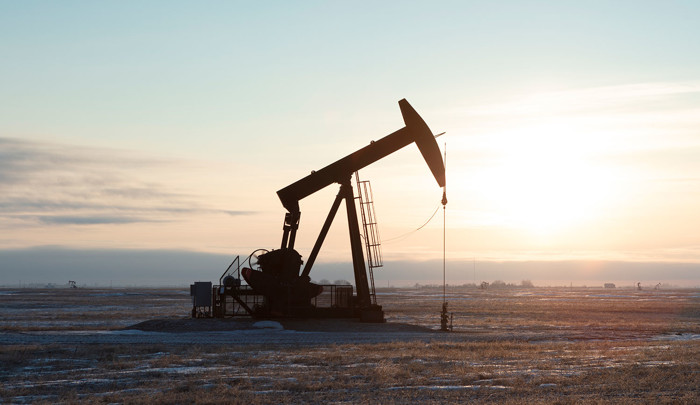
Lithium Extraction
You may also be interested in: